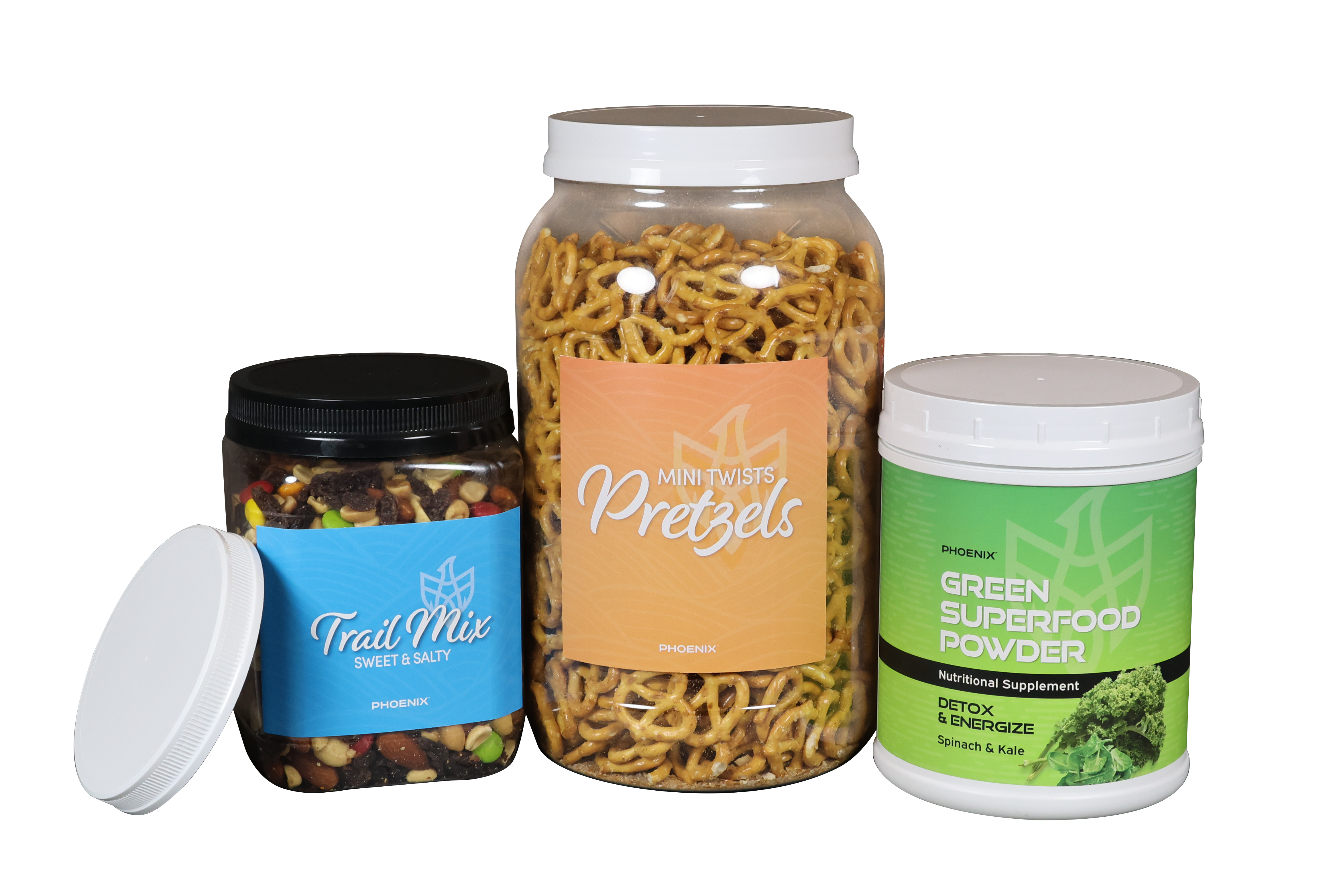
Stacking Up Our Impact on the Environment
The basic technology behind a plastic closure hasn’t changed. Threads on a bottle meet threads on a cap which twist together to create a reliable and secure seal. You may think that this basic principle of closure design is a formula that is repeated for every size, shape, and color. In reality, innovation and modification are an integral part of continuously improving the function, fit, and ultimately, the reuse of a closure.
The world has made more demands of packaging over the last fifty years. While the primary purpose of keeping products sealed and secure hasn’t changed, the packaging itself has gotten more attention for the experience we have when we open, close, and dispose of it. The demand for sustainability and responsible material consumption requires out-of-the-box thinking on how closures are manufactured, the materials used, and even how caps are shipped to the manufacturer.
As an initial effort to design closures that contribute to less waste in 2017, PHOENIX looked at right-weighting our largest diameter caps. By using the least amount of virgin resin as possible without jeopardizing quality and integrity of the cap, the lighter weight would result in less plastic waste. The result of this redesign resulted in EcoStack®, a continuous thread closure that uses less resin in an innovative, stacked design.
Stacking the 120mm closures, the pack count increased as much as 87% and allowed more closures per carton. This created a reduction of greenhouse gas emissions when it came to shipping our product to PHOENIX customers. PHOENIX estimates that this substantial increase reduced the number of trucks on the road by over 100 in the first five years of EcoStack sales.
The new stacked designed created a waterfall of additional positive change. Using less resin and optimizing the wall thickness of the closure resulted in a more efficient molding process and shorter cooling time, thus using less energy and water consumption. For PHOENIX customers, the stacked design holds the cap in place and provides structure in transit resulting in a flatter cap that is easier to apply on a filling line. Using less energy to manufacture, less fuel to ship, and less down time on a filling line for our customers, PHOENIX EcoStack closures make a big impact on the sustainability bottom line.
EcoStack also receives points for style. The new design offers a more modern and clean aesthetic which helps our customer’s brand look fresh and exciting. The great news is that EcoStack is being developed for more sizes. This groundbreaking technology will soon be available in 70mm, 83mm, and 89mm sizes in addition to the existing 110mm and 120mm closures.
PHOENIX is transforming packaging by continuing to innovate closure technology. The simple concept of keeping products fresh and secure can be done with integrity and responsibility with incremental and impactful changes.